Extreme weather that whips up strong winds, releases torrents of rainfall and causes floods, droughts and other hazards is becoming more common, and businesses in the shade industry have had to adapt. They have introduced new structures, fabrics, finishes and cleaning products to help consumers keep their canopies, shade sails, awnings and other shade structures intact and looking sharp. However, the trend toward more extreme weather patterns has also changed the market a bit.
“To better meet environmental factors, shade structures increasingly—up to 70%—have moved towards fixed-frame structures with no fabric, due to the benefit of extended longevity,” says Victor Jensch, vice president of market development at Ennis Fabrics, headquartered in Edmonton, Alta., Canada. He notes that over the past 10 years, sales of fixed-frame structures without fabric increased from being only a 25% share of the residential market. The change has affected the commercial market as well, although at a slower rate.
“Fabric manufacturers are fighting for a smaller piece of the pie, so prices are becoming more competitive, and most are seeing a decline in revenue,” Jensch says.
Shade structures that still have fabric include fixed frame structures with permanent or removable fabrics and retractable awnings with or without additional framework. “These have all developed in their own right to meet both fashion and environmental demands,” he says.

Focusing on strength
Shade structures have improved from painted steel and cast-iron posts to aluminum, hot-dipped galvanized or metalized steel, and other steel products to withstand the elements and prevent oxidation, Jensch adds.
In the face of storms and other inclement weather, shade structures have become better equipped. “Fiber and fabrics have moved from prioritizing UV with an emphasis on preventing color fading, to also prioritizing increased tensile and tear strength capabilities, both before and after extended UV exposure,” he says.
He adds that customers purchasing fabrics in more extreme climates such as Australia and New Zealand have started to recognize that shorter fabric lifespans and earlier replacement are increasingly necessary. “The challenge for all fabric manufacturers is to address the limitations of the chemical compounds that make up the yarns and to construct new fabrics with greater strength characteristics,” he says.
He notes that among woven fabrics, solution-dyed acrylic has the longest lifespan against UV exposure but is inherently weaker than polyester or olefin (polypropylene), both of which start much stronger but do not last as long after ongoing weathering.

Improving finishes and fabric
Another goal of manufacturers is to develop better finishing products. “Emphasis has increased on the development of finishing of these fabrics,” Jensch says. “For example, the addition of proprietary UV inhibitors in the after-treatment process [is intended] to extend the strength of polyesters. Other developments are in fabric construction and may include the blending of acrylic, polyester and olefin to maximize strength and minimize weathering.”
He adds that “larger commercial shade structures have remained largely unchanged: fixed framework with pre-constraint high-tenacity polyester yarns coated with PVC or acrylic.”
Dan Neill, owner of J. Miller Canvas LLC in Santa Ana, Calif., agrees with Jensch that fabrics are changing to meet evolving environmental needs. “The materials used for shade structures have evolved from canvas to vinyl, acrylic, polyester and high-density polyethylene [HDPE],” Neill says. “These modern fabrics are more durable, resistant to fading, wear and tear, and mildew development.”

Neill also sees increased use of durable, weather-resistant and customizable tension membrane structures. “These structures can be engineered to meet various design requirements, including increased wind resistance and fire-safety considerations,” Neill says.
One company innovating new products to cope with devastating storms is Twitchell Technical Products LLC in Dothan, Ala. It has developed OmegaTex™, which it calls “the original hurricane screen.”
OmegaTex incorporates aramid fibers, materials identical to those used in making bulletproof vests and other types of protective gear. The fabric also features a PVC compound specifically developed by the company to increase durability against UV radiation, microorganisms and prolonged exposure to the environment. A spate of high-powered storms hitting the southeast U.S. spurred the company to create the fabric.
“Twitchell recognized a void in the market as they observed the increasingly stronger and intense storms that were wreaking havoc on homes in the Gulf of Mexico region,” says Gena Webb, vice president of research and development and products at Twitchell.

Enhancing stability and longevity
Like Jensch, Neill says there is more focus on improving the design of outdoor shade structures to enhance their stability and longevity, which includes features such as reinforced seams, additional structural bracing and innovative tensioning systems
for shade sails.
Technology is being incorporated into retractable awnings, and shade structures now are equipped with weather sensors and automation systems. “These systems can detect changes in weather conditions such as strong winds or heavy rain and automatically retract the awning or adjust the tension of shade sails to prevent damage,” Neill notes. Jensch adds that powder coating technologies are being used on retractable-awning hardware to make them resistant to weathering.
In areas such as Southern California, where wildfires are a threat, outdoor shade structures may be coated with fire-resistant materials to reduce the risk of ignition. “This can include flame-retardant treatments applied to fabrics or specialized coatings for metal frames,” Neill says.
In addition, some outdoor shade structures are designed to be modular and portable for easy assembly, disassembly and relocation as needed. “This flexibility enables users to adapt to changing weather conditions or move the structure to a safer location during extreme weather events,” Neill says.

Looking to the future
As they look forward, Neill and Jensch see growing emphasis on creating environmentally friendly shade products. Jensch anticipates products being developed that are free of PFAS. He also sees a focus on developing shade elements that are easy to clean and water-resistant. He believes there also will be more focus on consumer training to maintain the finished shade structures, including cleaning practices, cleaning chemicals and UV- and water-resistance reapplication at preset periods during the life of the structure.
But natural fabrics can’t yet replace engineered ones, he says, for “longevity of strength requirements for outdoor awnings. This leaves us with synthetic options only at this time.”
With severe weather events and other elements that can dirty shade structures, such as bird droppings, wildfire smoke, and increased pollen in the air due to earlier, warmer temperatures and more CO2 in the atmosphere, Neill says customers should follow manufacturers’ guidelines for proper cleaning methods and conduct regular inspections to ensure structural integrity. “We should expect to see further advancements in fabrics, cleaning methods and installations of fabric shade structures to address evolving weather challenges,” he says. “Future fabrics may incorporate self-cleaning properties such as hydrophobic coatings to repel dirt, water and pollutants more effectively, reducing the need for frequent
manual cleaning.”
Even with the development of more weather-resistant products, owners of shade structures may have to adjust their expectations for how long one will last and how much care it will need. “In the past, structures could be left to exist without any tender loving care,” Jensch says. “In the future, consumers will need to follow an annual cleaning and reapplication procedure to help their awnings last longer.”
Annemarie Mannion is a freelance writer based in Willowbrook, Ill.
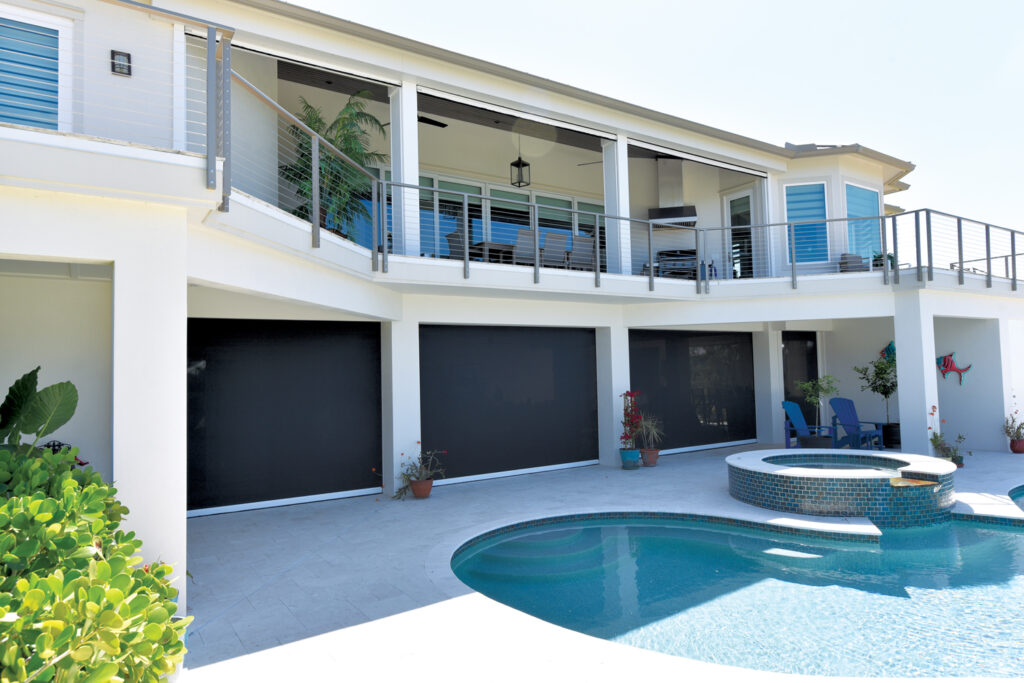
What goes into creating a hurricane-resistant product? A lot of testing, according to Twitchell Technical Products LLC, a more than 100-year-old company in Dothan, Ala., which couldn’t label its product OmegaTex™ as hurricane-resistant without empirical proof.
One test the product underwent was the High Velocity Hurricane Zone shot test. This test required the fabric to withstand a 9-pound two-by-four being shot at it from an air cannon using compressed air at 80 feet per second, both in the center of the screen and in the corner.
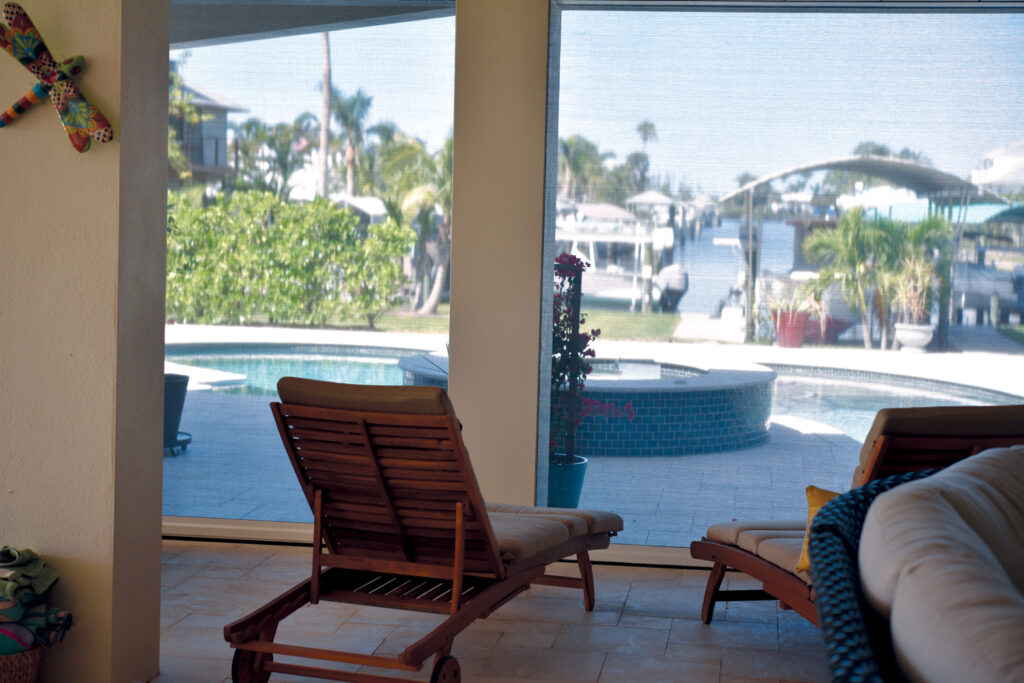
The testing was approved by the Miami-Dade Notice of Acceptance, a product certification Miami-Dade County offers that is accepted throughout Florida. The Florida Product Approval system also accepted it.
Beyond testing, Gena Webb, vice president of research and development and products at Twitchell, says the screen also stands up well in real-life conditions. OmegaTex’s effectiveness was demonstrated when Ian, a Category 5 storm, struck Florida in 2022, and a house equipped with the OmegaTex screens survived intact. “Astonishingly, the house withstood the full force of the hurricane without any damage,” Webb says. “This is particularly remarkable, as the same family had suffered from the complete devastation caused by Hurricane Andrew in [1992].”
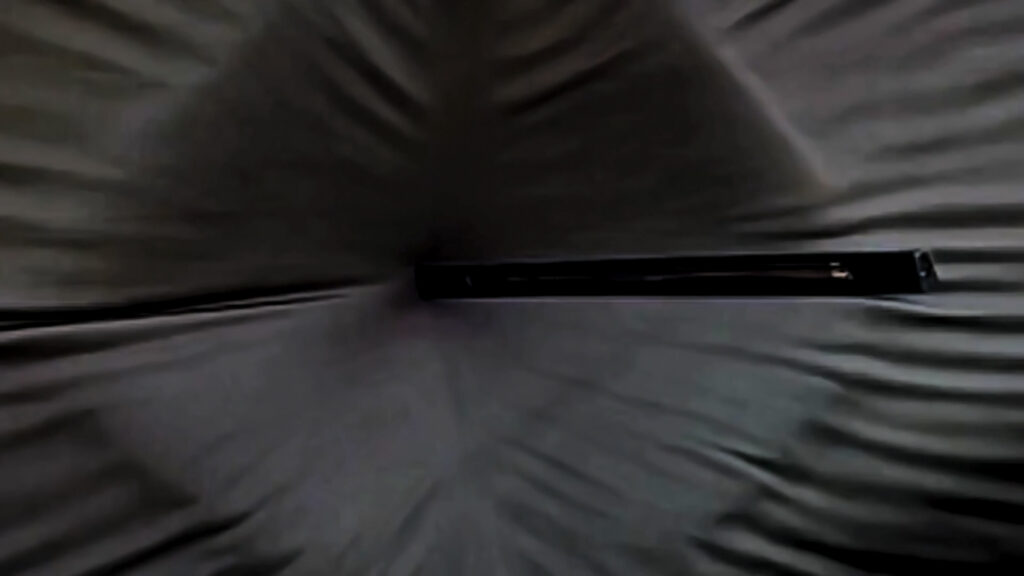
To be able to call a product “hurricane resistant” in Florida involves certification testing that includes shooting a two-by-four at the material. Above is a still image from a test video. Images: Twitchell Technical Products LLC
Leave A Comment